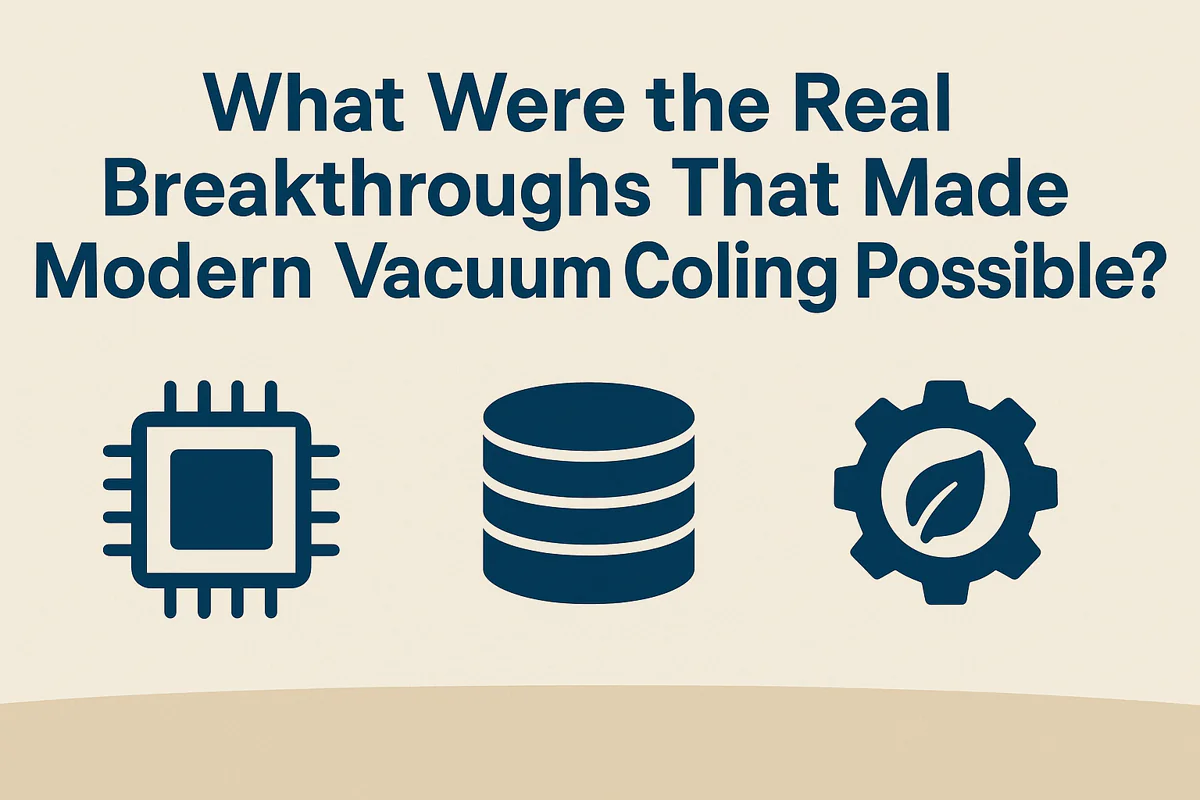
What Were the Real Breakthroughs That Made Modern Vacuum Cooling Possible?
You look at today’s advanced vacuum coolers and see a fast, reliable, and almost automatic process. It’s easy to take for granted. But this level of performance didn’t happen by accident. It’s the result of several major technological leaps that transformed the industry.
The history of modern vacuum cooling is a timeline of key breakthroughs: integrating global top-brand components, developing smart PLC-based controls, customizing designs for specific industries, and building-in advanced safety and efficiency systems.
These advancements didn’t occur in isolation. They built upon each other, turning a basic scientific principle into the high-tech, indispensable tool we offer today. For a professional buyer like Norman or a hands-on owner like Carlos, understanding these breakthroughs is key to knowing why a modern Allcold machine is a sound investment. Let’s trace this path of innovation.
When did machines stop being a local affair?
Early industrial machines were typically built using components from a single region or even a single company. While this was simple, it created a huge bottleneck. The machine was only as good as its weakest part. If a manufacturer made a great chamber but a poor vacuum pump, the entire system’s performance suffered.
A major breakthrough was the shift to a global sourcing model. Modern machines are now assembled using the best possible components from specialized world-leading brands, ensuring every single part is of the highest quality and reliability.
This was a complete change in manufacturing philosophy. The goal became achieving ultimate performance, not just relying on local suppliers. When I design an Allcold vacuum cooler, I see myself as an integrator of global excellence. We build the robust stainless steel chamber at our facility in Dongguan, China, but the heart and soul of the machine come from engineering giants. The powerful vacuum pump might come from Leybold in Germany, while the critical refrigeration compressor is a high-performance unit from Bitzer, also from Germany. The precision expansion valve that regulates the refrigerant is from Danfoss in Denmark, and critical safety components like phase protection relays are sourced from Carlo Gavazzi in Switzerland. This "best-of-breed" approach is a massive leap forward. It means the system isn’t compromised. Every component, from the compressor and pump down to the AC contactors from Schneider, is chosen for its superior performance and durability. This milestone ensures that customers receive a machine that is not just a sum of its parts, but a synergistic system optimized for power, reliability, and a long service life.
The International Team Inside Your Cooler
Breakthrough Area | Component | Brand | Country of Origin |
---|---|---|---|
Refrigeration Power1 | Compressor | Bitzer | Germany |
Vacuum Creation | Vacuum Pump | Leybold | Germany |
Precision Control2 | Expansion Valve | Danfoss | Denmark |
System Protection | Phase Protection | Carlo Gavazzi | Switzerland |
Electrical Reliability | AC Contactor | Schneider | Germany |
How did machine intelligence replace manual guesswork?
Imagine trying to cool a product by manually flipping switches and watching analog needles, hoping you get the pressure and temperature right. That was the reality for early equipment operators. It was inefficient, inconsistent, and required a highly skilled operator to get decent results. The process was more art than science.
The greatest breakthrough in usability was the integration of a PLC (Programmable Logic Controller) with a simple touch screen interface. This automated the entire cooling cycle, providing perfect, repeatable results every time.
This leap into digital automation changed everything. The "brain" of a modern Allcold cooler is now a powerful Siemens PLC3, a rugged industrial computer that we program with the precise parameters for a customer’s specific needs. The operator no longer needs to be a technical expert. They simply use the touch screen control, which clearly displays the vacuum level, product temperature, and elapsed time. This makes operating a complex piece of machinery incredibly simple and foolproof. But the intelligence goes much deeper. For instance, the system now includes a "troubleshooting assist system4" that can help diagnose issues without needing an engineer on-site. We can also program features like a "vacuum delay facility," which automatically adjusts the cycle for products with high water resistance, ensuring the entire load cools uniformly. This level of smart, adaptive control is a world away from the old manual systems. It guarantees consistency, which is critical for food safety and quality, and it reduces the need for constant, skilled supervision, freeing up valuable staff. This breakthrough put true process control directly into the hands of the user.
When did one size stop fitting all?
In the past, industrial equipment was often generic. A farmer or a baker would buy a cooling machine and then have to figure out how to make their product work with it. This often led to compromises in quality and efficiency because the machine wasn’t designed for their specific product or workflow.
A pivotal breakthrough was the development of tailor-made designs. The technology evolved from a generic concept into highly specialized machines built to meet the exact requirements of different products, like baked bread or steamed rice.
This shift was driven entirely by listening to my clients. The needs of a baker in Hungary are completely different from a rice producer in Poland or a vegetable farmer in Mexico. A baker needs to cool 200kg of bread from 92°C to 30°C in just 5 minutes using specific trolley dimensions of 760x610x1800mm. A producer of steamed rice needs to cool their product from 98°C to 3°C in about 15-25 minutes. These different starting temperatures, target temperatures, cooling times, and handling methods (pallets vs. trolleys) required a radical new approach. The breakthrough was to stop selling a standard box and start providing custom solutions5. We now design the vacuum chamber dimensions6, the refrigeration capacity, and the vacuum pump power based on the customer’s exact product, batch weight, and desired cycle time. This ensures the machine is not oversized and wasting energy, nor undersized and failing to meet production targets. This move to "plentiful tailor-made options" represents a crucial point in the technology’s timeline, transforming it from a rigid piece of hardware into a flexible, adaptable production solution that integrates seamlessly into a customer’s existing process.
How did safety and efficiency become standard features?
Early industrial machines were often designed with a single purpose: get the job done. Operator safety and energy consumption were frequently secondary concerns. These machines could have exposed moving parts, basic electrical systems, and motors that ran inefficiently, costing the owner a fortune in electricity bills.
The modern breakthrough was to engineer safety and efficiency directly into the machine’s core design. This includes comprehensive electrical protection systems and high-efficiency components that minimize power usage and protect operators.
This evolution reflects a maturing of the technology. A powerful machine is only useful if it’s safe to operate and affordable to run. On the safety front, we’ve integrated multiple layers of protection. This starts with clear warning pictograms for things like hazardous voltage or entanglement hazards. It also includes physical hardware like Schneider emergency stop buttons and safety relays7 that can instantly de-energize the machine. We go even further by including advanced electrical protection, like phase protection relays that guard the motors against damaging power fluctuations. On the efficiency front, the breakthrough came from a holistic system approach. Instead of just using a bigger motor, we use high-efficiency evaporators8 and air-cooled condensers. This allows us to get the maximum cooling effect from the refrigeration compressor, minimizing its required kilowatt rating. Furthermore, modern systems have intelligent power-saving features. If the machine is left idle for a period, it will automatically shut down to save electricity and will only restart when the operator presses the start button. This focus on building a safe, reliable, and energy-conscious machine is a defining characteristic of today’s advanced vacuum coolers.
Conclusion
The timeline of vacuum cooling is marked by these crucial breakthroughs. By integrating global components, intelligent automation, custom designs, and a deep focus on safety and efficiency, the technology has transformed into the powerful and reliable production tool that modern businesses demand.
-
Explore this link to discover cutting-edge technologies that enhance refrigeration efficiency and performance. ↩
-
Learn how Precision Control can optimize your refrigeration systems for better performance and energy savings. ↩
-
Explore this link to understand how Siemens PLCs revolutionize automation, enhancing efficiency and control in various industries. ↩
-
Discover how troubleshooting assist systems can streamline operations and reduce downtime, making machinery management easier. ↩
-
Exploring this resource will reveal how tailored solutions can enhance efficiency and meet specific client needs. ↩
-
Understanding this concept is vital for optimizing cooling systems and improving production efficiency. ↩
-
Understanding safety relays is crucial for ensuring machine safety and compliance in industrial settings. ↩
-
Exploring high-efficiency evaporators can enhance your knowledge of energy-saving technologies in refrigeration. ↩
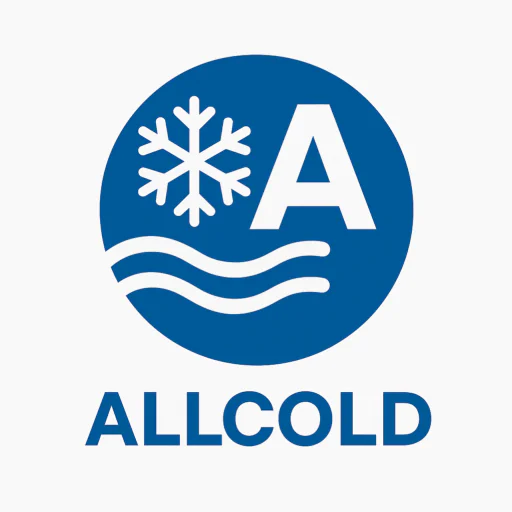
Mila
You May Also Like
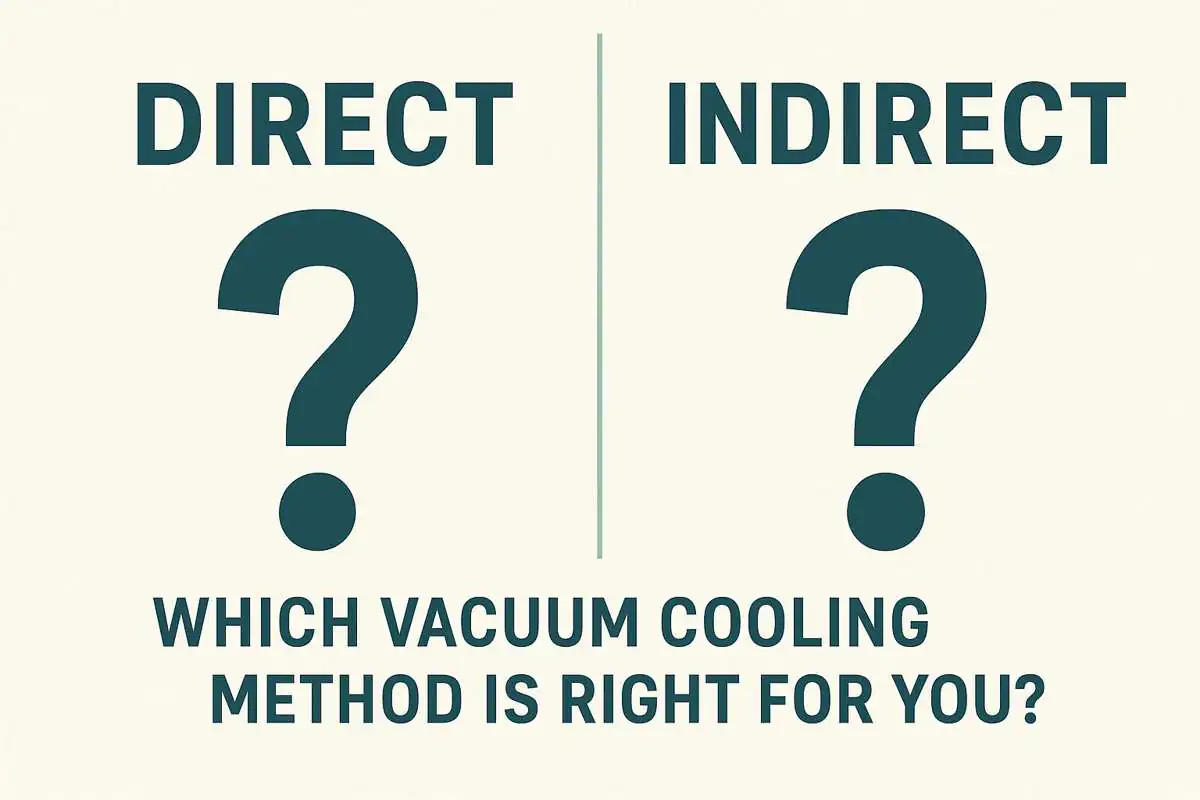
Direct vs. Indirect: Which Vacuum Cooling Method is Right for You?
You’ve decided on vacuum cooling, but a hidden technical choice emerges: direct or indirect cooling. This single design decision can
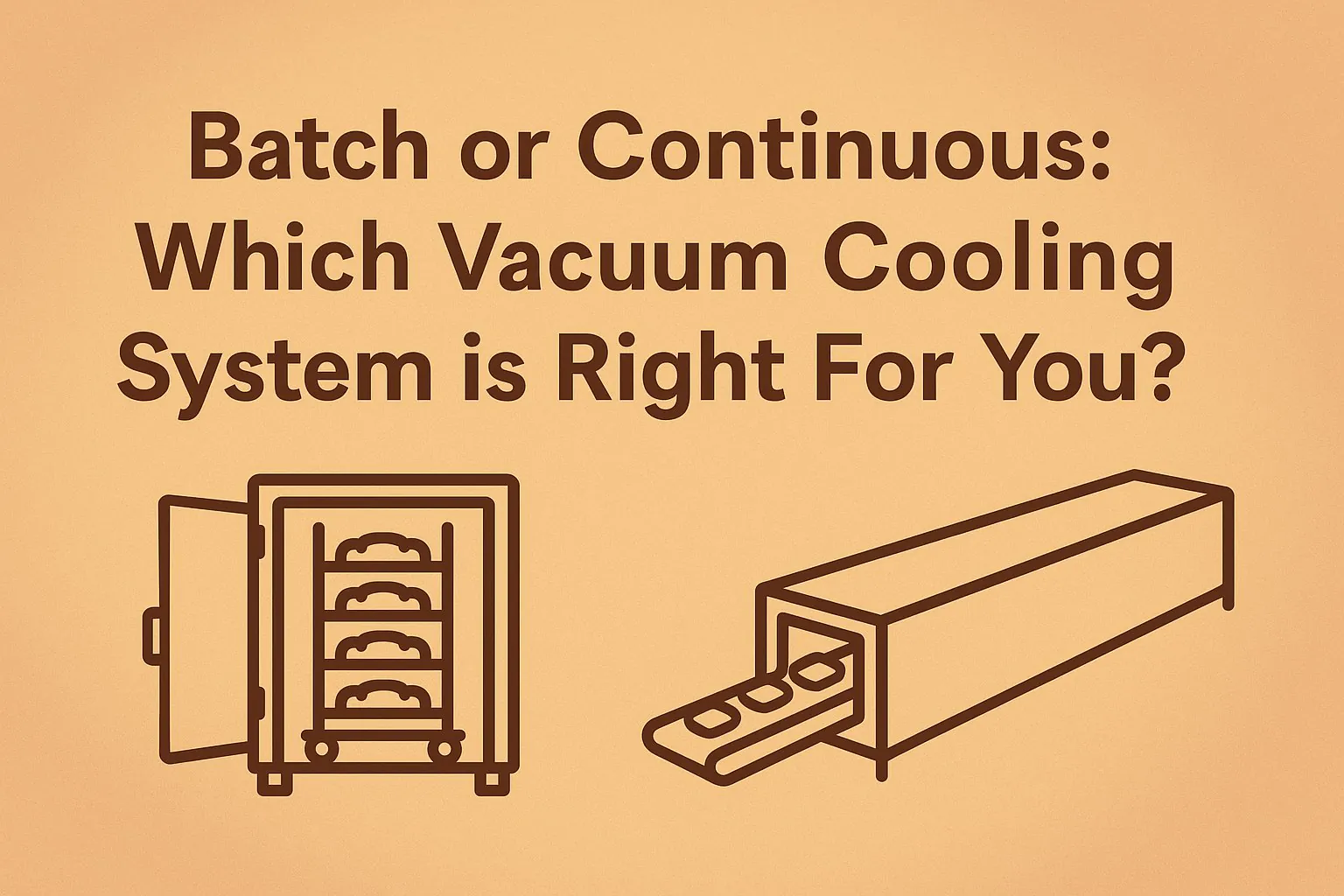
Batch or Continuous: Which Vacuum Cooling System is Right For You?
Choosing a major piece of equipment can be daunting. You know you need vacuum cooling, but then you see terms
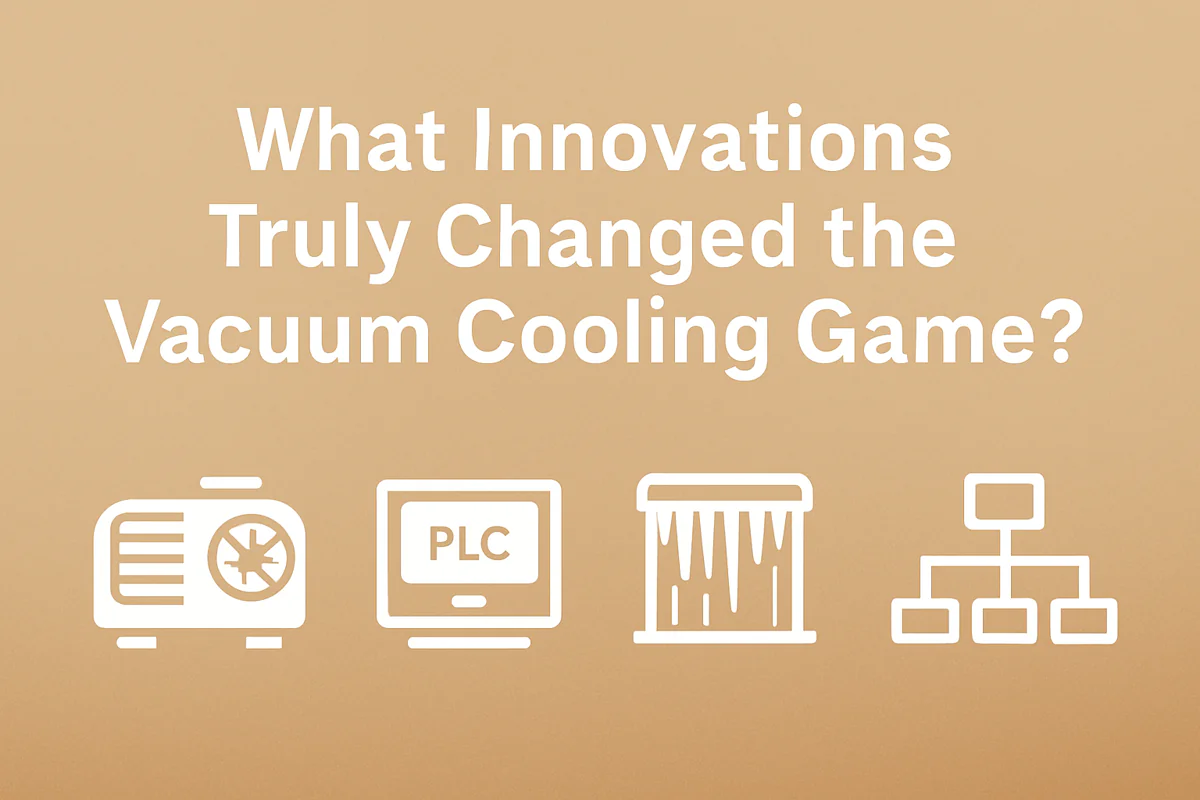
What Innovations Truly Changed the Vacuum Cooling Game?
You see a modern, stainless steel vacuum cooler operating flawlessly and it looks simple. But behind that easy operation are
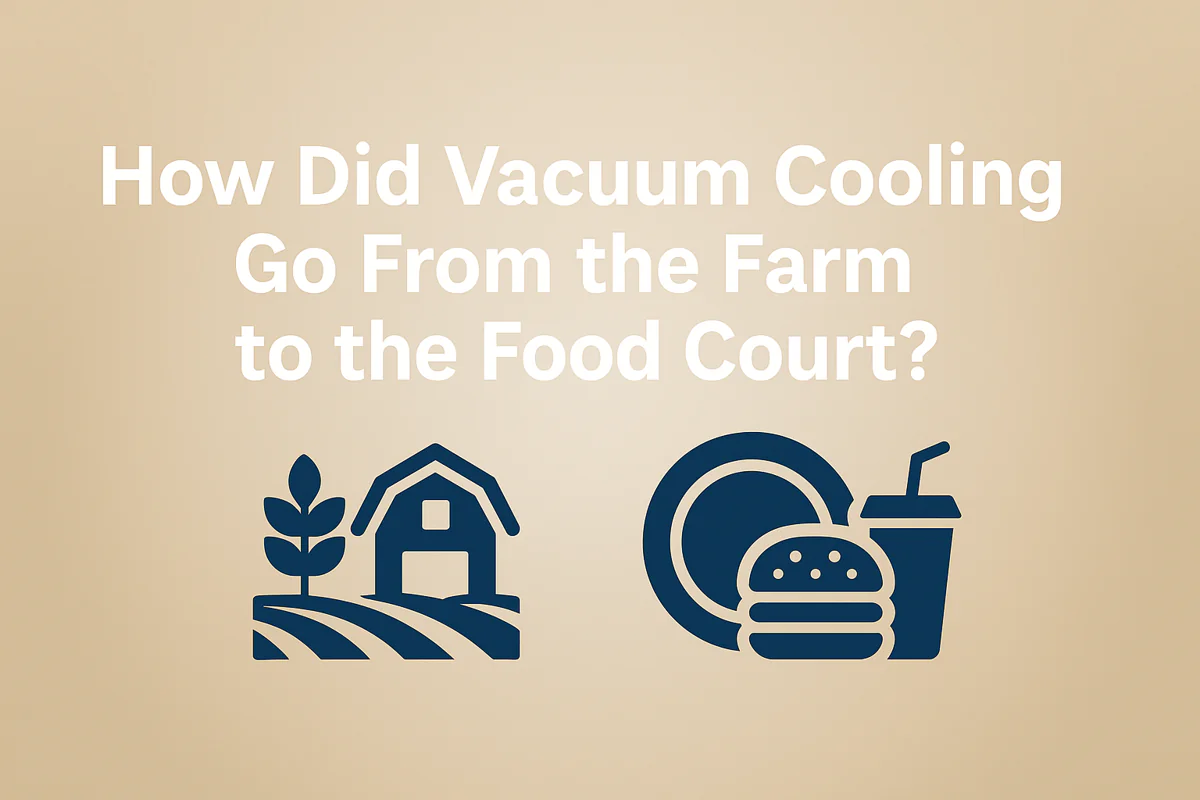
How Did Vacuum Cooling Go From the Farm to the Food Court?
You see a vacuum cooler in a modern bakery and think it’s a kitchen appliance. This powerful technology actually started
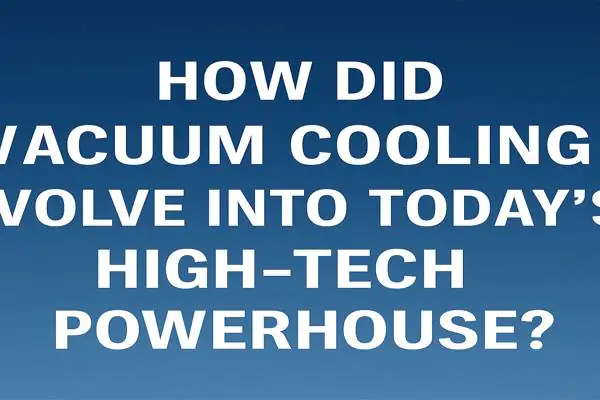
How Did Vacuum Cooling Evolve into Today's High-Tech Powerhouse?
You see a modern vacuum cooler: a sleek, stainless steel chamber with a complex control panel. You know it works
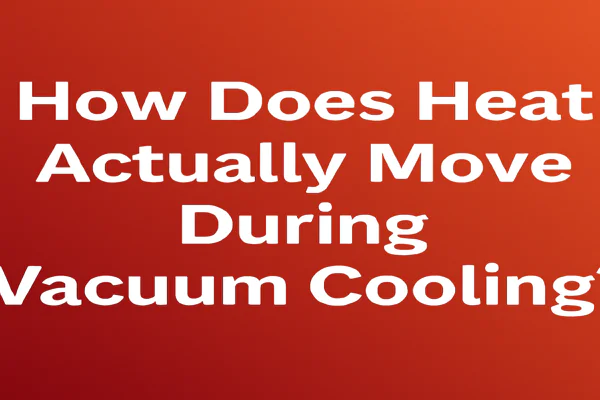
How Does Heat Actually Move During Vacuum Cooling?
You have a big challenge: a mountain of product, full of heat. You know that getting this heat out quickly
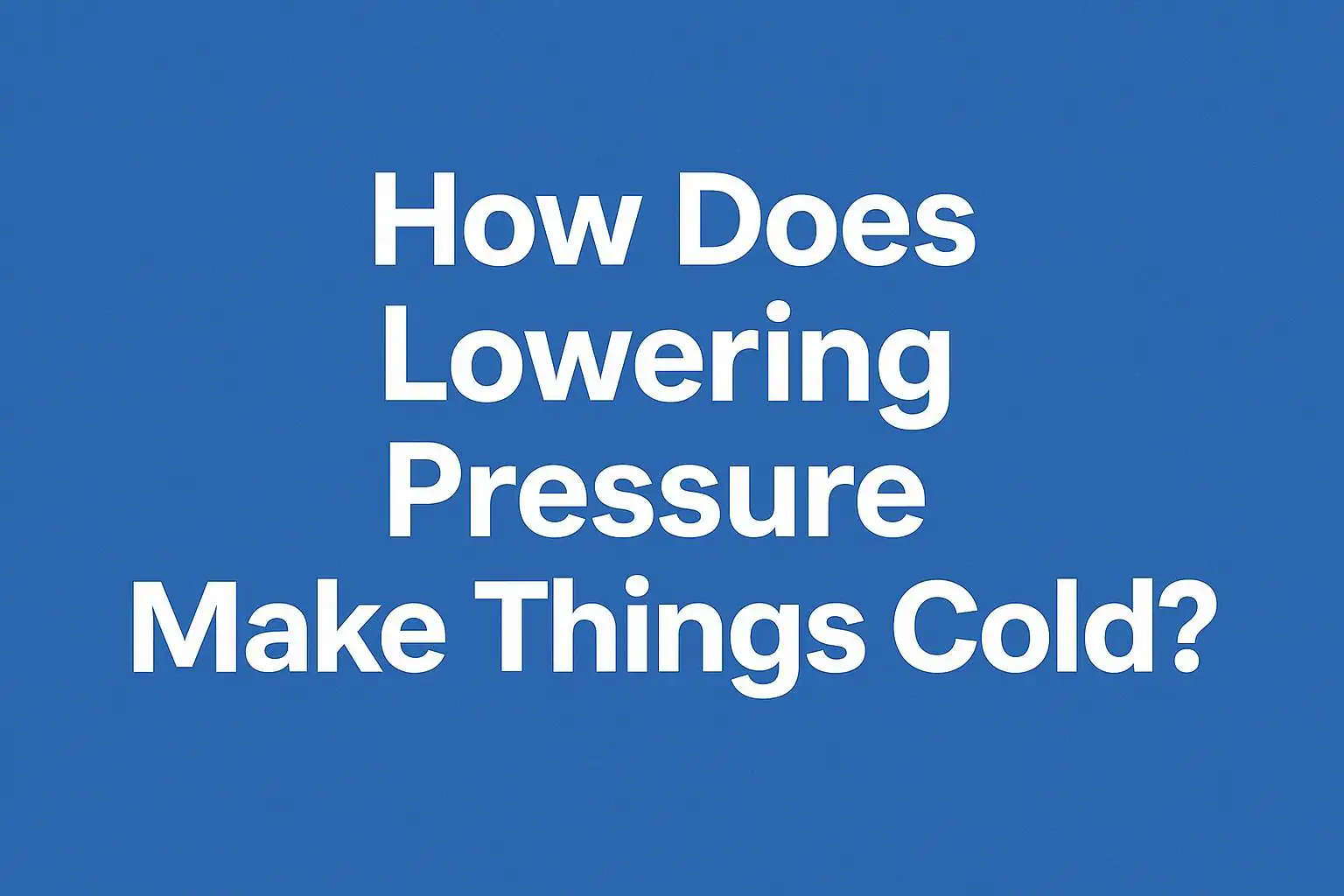
How Does Lowering Pressure Make Things Cold?
You look at the control panel of a vacuum cooler, seeing a pressure gauge dropping while a temperature gauge follows
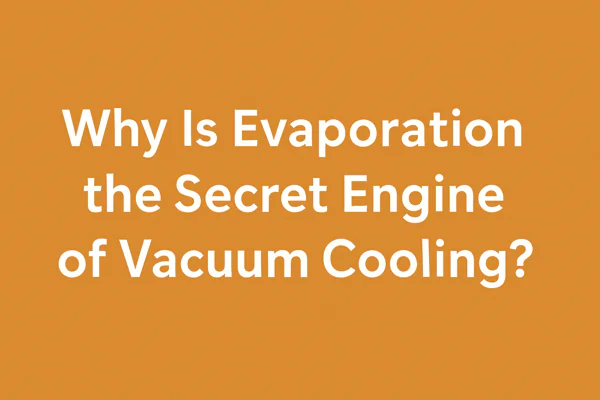
Why is Evaporation the Secret Engine of Vacuum Cooling?
You see a pallet of hot, freshly baked bread or warm, just-picked spinach. You know that slow cooling means lower
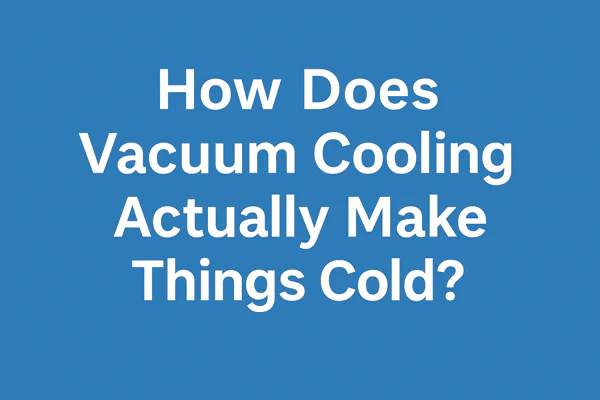
How Does Vacuum Cooling Actually Make Things Cold?
You’re looking at a pallet of freshly harvested lettuce, warm from the field. You’re told a machine can make it
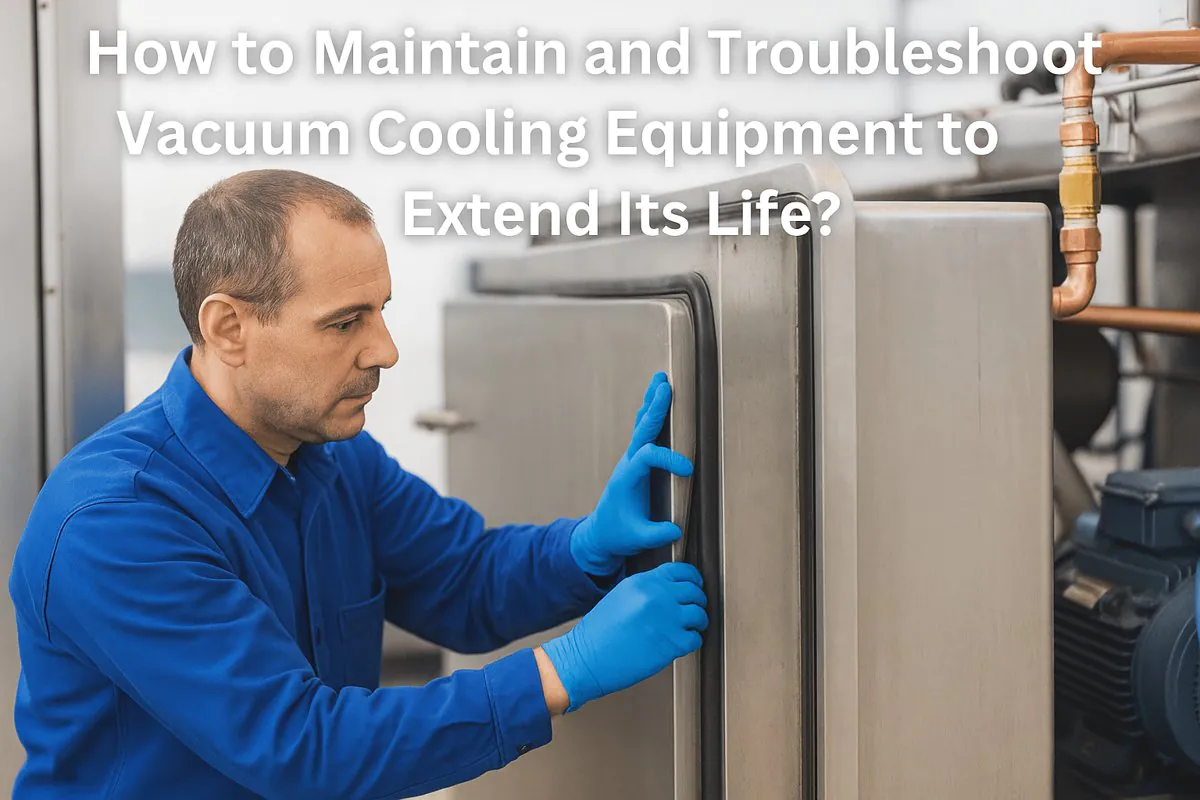
How to Maintain and Troubleshoot Vacuum Cooling Equipment to Extend Its Life?
Has equipment breakdown during peak seasons cost you dearly? Neglecting regular maintenance often leads to unexpected and costly downtime. Effective