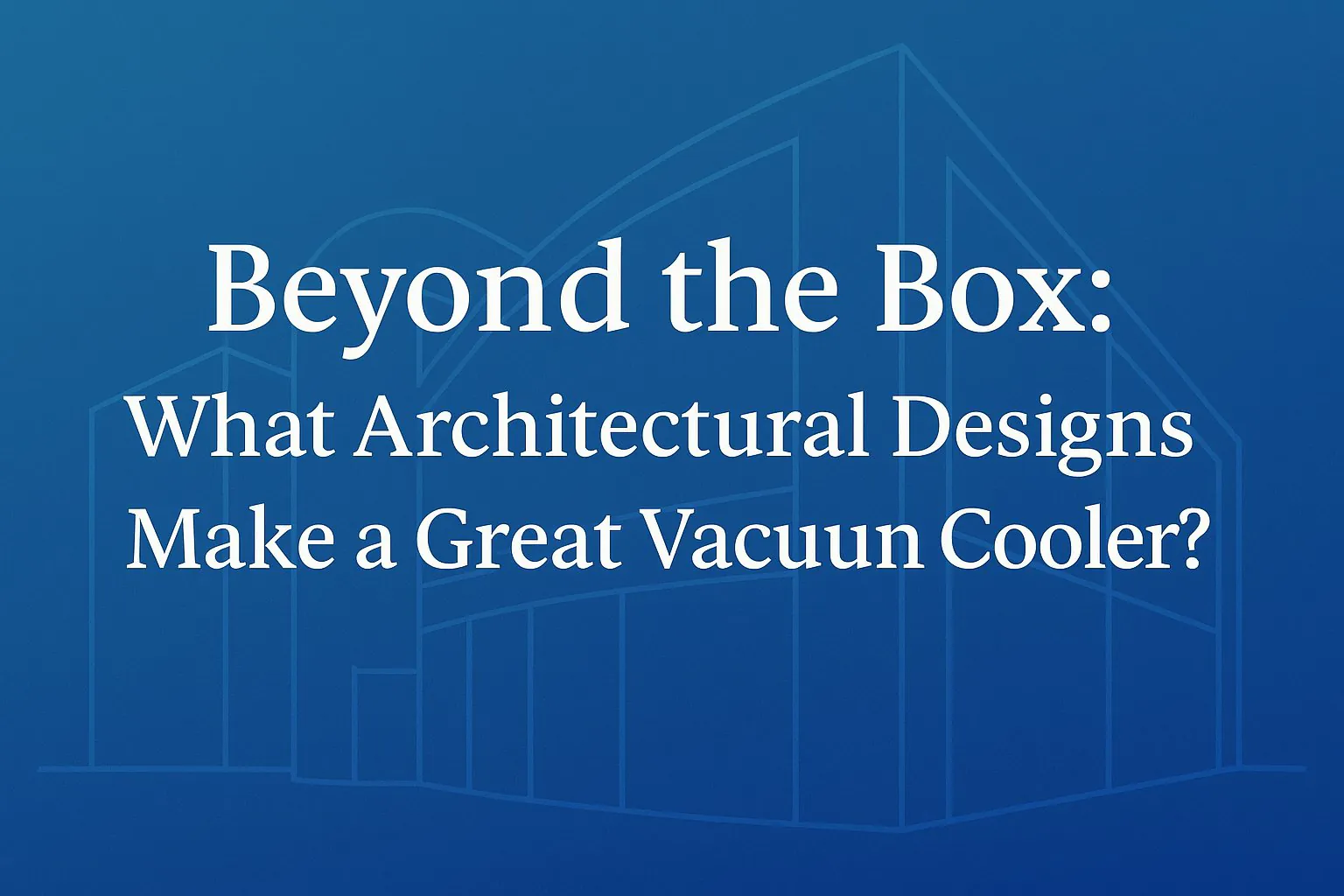
Beyond the Box: What Architectural Designs Make a Great Vacuum Cooler?
You’re looking to invest in a vacuum cooler, and many of them look the same: a simple steel box. But the hidden architectural designs—how it’s built and what’s inside—are what separate a reliable, high-performing machine from a constant headache.
A vacuum cooler’s architecture is its core design, covering the chamber’s physical layout, the type of refrigeration system, and the control software. Key designs include pallet vs. trolley chambers, advanced condenser types, and smart PLC controls, each impacting workflow and final product quality.
%[An infographic showing a cutaway view of a vacuum cooler, with callouts pointing to the chamber, compressor, condenser, and PLC screen.](https://allcoldcooling.com/wp-content/uploads/2025/07/vacuum_cooler_infographic_800x533.png”Key Architectural Components of a Vacuum Cooler")
I often tell my clients that buying a vacuum cooler is like building a house. The foundation and structure are invisible when it’s done, but they determine its strength and livability. Let’s dig into the key architectural designs that truly define a machine’s performance and value.
Pallets or Trolleys: How Should You Load Your Chamber?
Getting your product into the machine seems trivial, but the daily workflow of loading and unloading has a huge impact on your efficiency. The wrong chamber design can create bottlenecks that slow down your entire operation.
Pallet-based systems are designed for high-volume, forklift-loaded operations, like cooling harvested produce. Trolley-based systems are built for batch-processed foods, such as baked bread, offering more manual control and flexibility.
Designing for Your Workflow
The first architectural decision we discuss is how you will physically move your product. Your choice here depends entirely on your process. For a farm owner like Carlos, harvesting thousands of pounds of vegetables, a large chamber designed for two or more pallets is the only way to go. Our [AVC-600-2 Pallets](https://bunzlprocessor.com/blog/2025/07/01/benefits-of-plastic-pallets-for-food-applications/?srsltid=AfmBOoojIF4b4Vx70sGqaYxtOrCyVUks7W3Q2kPBsXAe0uoxOgVP47ep)[^1]
model is a perfect example of this architecture. Its wide door and reinforced floor are built to handle the weight and speed of forklift loading, maximizing throughput during a busy harvest. In contrast, for a central kitchen manager like Sophia, the needs are different. She might be cooling baked bread, where products are carefully arranged on tiered racks. For her, we would design a machine like our AVCF-200
model, which is specifically built to accept single trolleys. A trolley-based system allows for more delicate product handling and can be integrated into a manual workflow where racks are moved from the oven, to the cooler, and then to the packaging station. This architecture is often more compact and fits better into the constrained floor plans of food processing facilities. The key is to match the loading architecture to your existing or desired workflow, not the other way around.
Design | Target User & Product | Key Benefit |
---|---|---|
Pallet System | High-volume produce farms | Maximum throughput, forklift compatible. |
Trolley System1 | Bakeries, Central Kitchens | Better handling for delicate batches, workflow flexibility. |
Air, Evaporative, or Water: Choosing the Right Condenser Architecture?
Your machine’s refrigeration system generates a lot of heat. Getting rid of it efficiently impacts your energy bill and performance. The choice between air, a hybrid evaporative system, or water is critical.
Air-cooled is simple and very low-maintenance. Evaporative condensers are a high-efficiency hybrid using air and water, ideal for saving energy in hot climates. Traditional water-cooled systems are powerful but require complex external cooling towers.
Matching Heat Rejection to Your Climate and Costs
Every vacuum cooler has a condenser to reject the heat pulled from your product. The architectural choice for this component is a crucial part of our customization process. Our standard and most common design uses a high-efficiency, air-cooled condenser2. This system is simple, reliable, and self-contained. Fans blow ambient air over the refrigerant coils, making installation easy—you just need good ventilation. It’s a robust architecture that we design to work perfectly in ambient temperatures up to +52°C.
However, for clients in very hot and dry climates, we often recommend an evaporative condenser3. This is an intelligent hybrid architecture. It works by spraying a small amount of water over the refrigerant coils while fans pull air through them. The rapid evaporation of this water creates a powerful cooling effect, much more efficient than using air alone. For a client like Carlos in Mexico, this could mean significant energy savings4 during the hottest months, as it reduces the workload on the Bitzer compressor.
The third option is the traditional water-cooled system5, which relies on a large, external cooling tower. While powerful, this architecture is the most complex and expensive, requiring significant plumbing, water treatment, and maintenance. A buyer like Norman would weigh the high efficiency of an evaporative system against its need for some water maintenance, but would almost always prefer it over the complexity of a full water-tower system. For most clients, air-cooled is the best blend of simplicity and performance, but the evaporative design is a powerful tool we use for specialized, high-efficiency applications.
System Type | Mechanism | Best For |
---|---|---|
Air-Cooled | Uses fans and ambient air to cool refrigerant. | Simplicity, reliability, low maintenance, most climates. |
Evaporative | Sprays water over coils while fans pull air through. | High-efficiency in hot/dry climates, energy savings. |
Water-Cooled | Pumps water from an external cooling tower. | Very large industrial applications, highest complexity. |
Simple Start or Smart Control: What Is the Brain of the Machine?
You might think you just need a start button, but for many products, a simple "on/off" vacuum pull is too aggressive. Uneven cooling or surface damage can ruin your product quality and hurt your bottom line.
Our machines are built with an advanced control architecture, featuring a Siemens touch screen and a programmable "vacuum delay facility". This allows for precise, gentle cooling cycles tailored to delicate products.
The Power of Programmable Control
The true intelligence of a modern vacuum cooler lies in its software architecture. While any machine can create a vacuum, a great machine can control it with precision. That’s why we use top-tier Siemens touch screens6 as the operator control center. This user-friendly interface allows my clients to do more than just start a cycle; they can customize and save "recipes" for different products. One of the most critical features we build into this control system is the "vacuum delay facility7". I recommended this for Sophia when she needed to cool freshly steamed rice. Rice has a very high water content, and a standard, aggressive vacuum can cool the outside so fast that it seals the surface, trapping heat and moisture in the core. The vacuum delay facility avoids this by pulling the pressure down in stages. It can automatically pause the process at an intermediate level, allowing the pressure and temperature to equalize throughout the entire batch before continuing down to the final temperature. This ensures perfectly uniform cooling, which is essential for food safety and quality. The same principle applies to baked bread, preventing the crust from becoming tough or damaged. This smart control architecture is not a luxury; for high-value or sensitive products, it is essential.
Standard Parts or Premium Components: Does Brand Name Matter?
All coolers use common parts like compressors and pumps. But the architectural philosophy of which specific brands to use has a massive impact on the machine’s day-to-day reliability and long-term serviceability.
Our design architecture specifies premium, globally recognized components. We use German Bitzer compressors, Leybold vacuum pumps, and Schneider electronics, ensuring reliability, longevity, and easy access to service parts.
An Architecture of Quality
A machine is only as reliable as its weakest component. This is why our core design philosophy is to build an architecture of quality from the ground up. If you look at our standard parts list for a machine like the AVC-600-2 Pallets
, you will see a commitment to this philosophy. The heart of the refrigeration system is a German Bitzer compressor. The heart of the vacuum system is a German Leybold pump. The electrical controls, contactors, and relays are from Schneider, another German leader. The critical expansion valve is from Danfoss of Denmark. For a buyer like Norman, this is incredibly important. His biggest pains are equipment downtime and finding qualified technicians. By using these world-class brands, we build a machine that is fundamentally more reliable. Furthermore, if a part ever does need service, a qualified refrigeration or electrical technician anywhere in the world will recognize these names and be able to source parts or perform maintenance. We are so confident in this quality-first architecture that every system is tested for 72 hours trouble-free before it even leaves our factory. Choosing premium components isn’t about bragging rights; it’s about providing our clients with peace of mind and the lowest possible total cost of ownership.
Conclusion
The best architecture isn’t about one feature. It’s how the chamber design, condenser system, smart controls, and premium components are integrated into one cohesive system that delivers reliable, perfect cooling for your specific product.
-
Discover how a Trolley System enhances workflow flexibility and product handling, ideal for bakeries and central kitchens. ↩
-
Explore the advantages of air-cooled condensers for efficient cooling solutions in various climates. ↩
-
Learn how evaporative condensers enhance cooling efficiency, especially in hot and dry climates. ↩
-
Find effective strategies for maximizing energy savings in cooling systems, crucial for cost efficiency. ↩
-
Discover the complexities and benefits of water-cooled systems for large industrial applications. ↩
-
Exploring Siemens touch screens can reveal their advantages in user interface design and operational efficiency. ↩
-
Understanding the vacuum delay facility can enhance your knowledge of food cooling processes and improve product quality. ↩
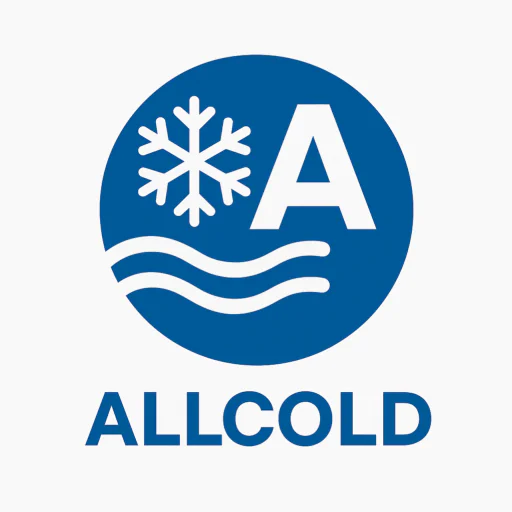
Mila
You May Also Like
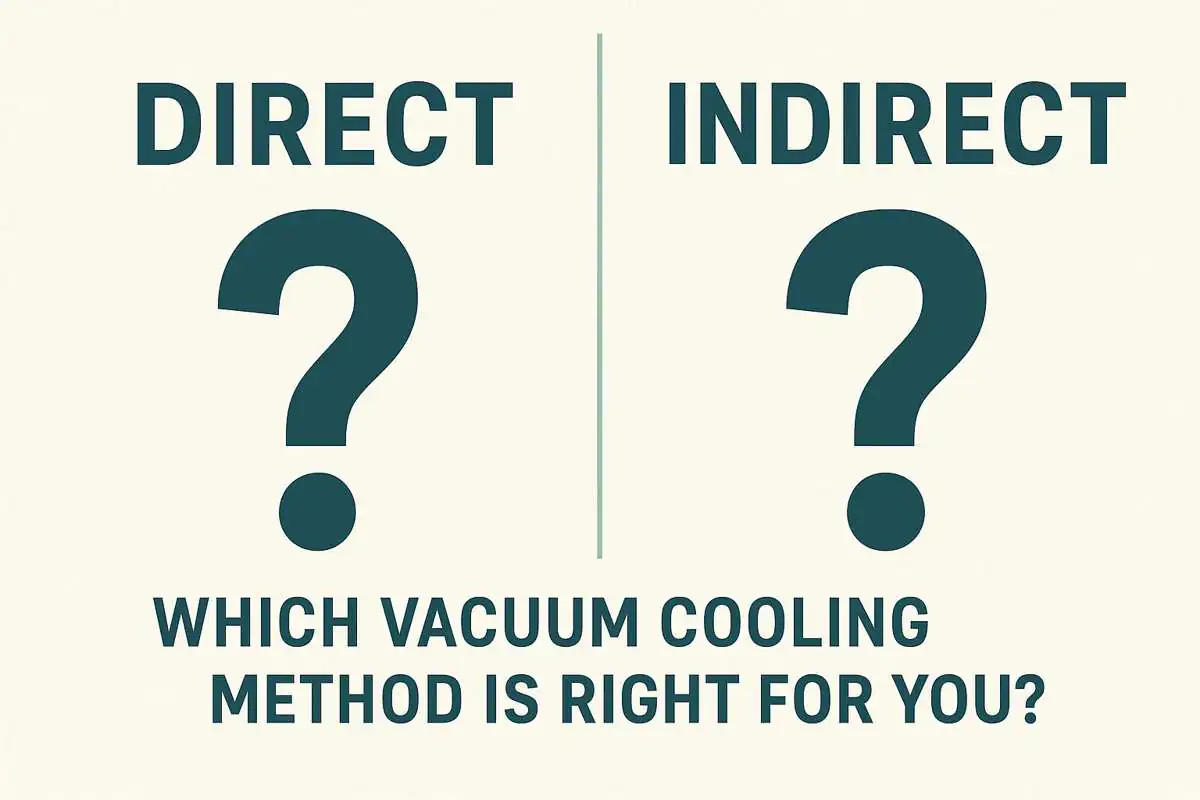
Direct vs. Indirect: Which Vacuum Cooling Method is Right for You?
You’ve decided on vacuum cooling, but a hidden technical choice emerges: direct or indirect cooling. This single design decision can
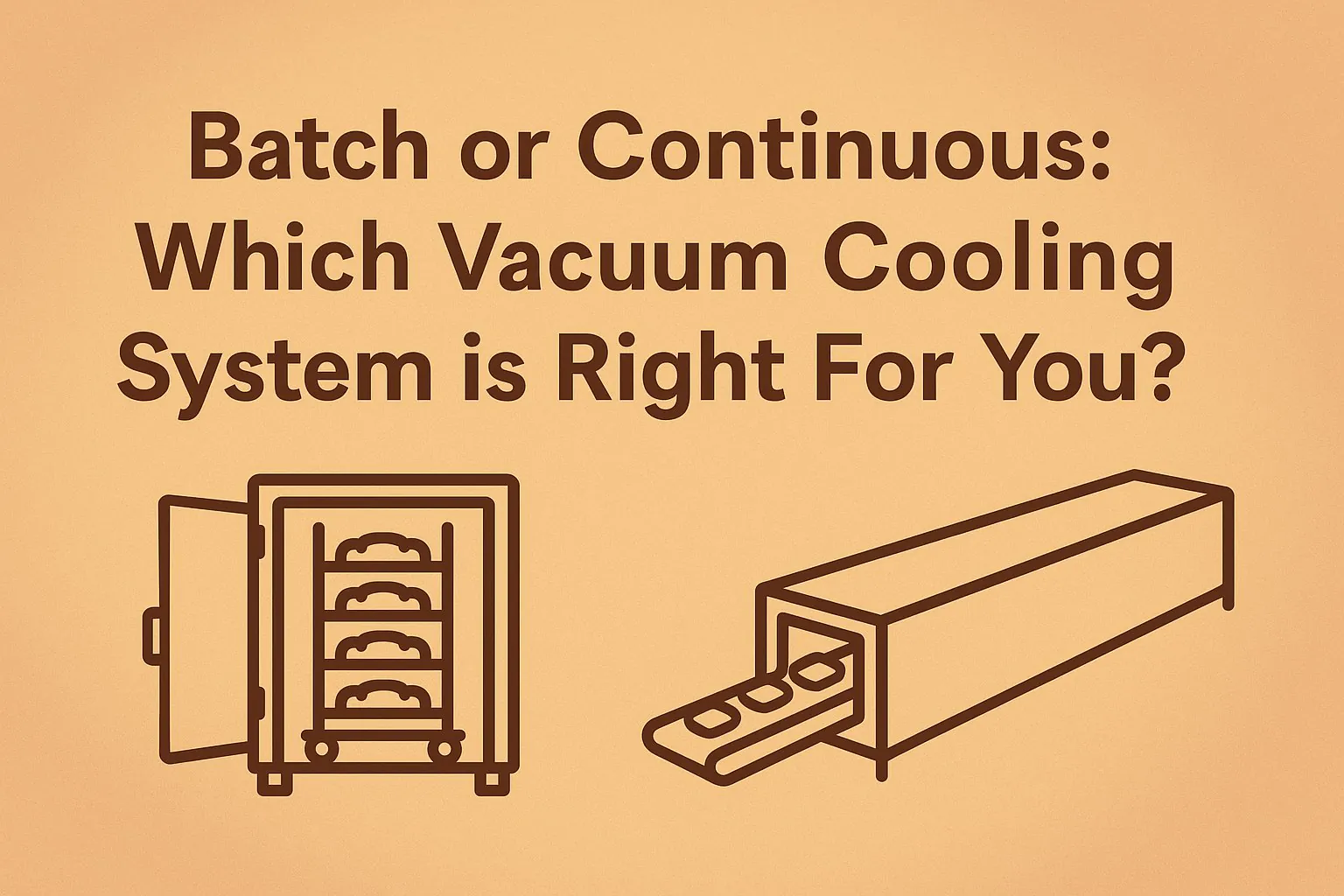
Batch or Continuous: Which Vacuum Cooling System is Right For You?
Choosing a major piece of equipment can be daunting. You know you need vacuum cooling, but then you see terms
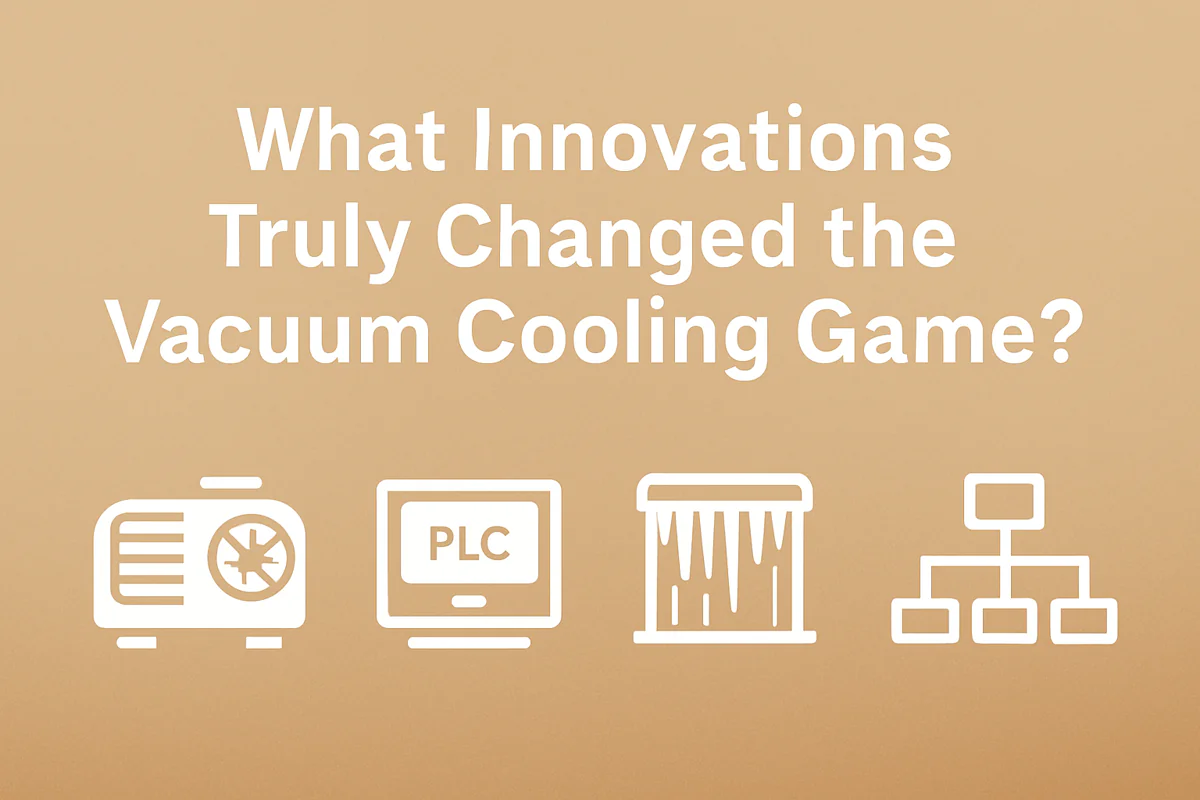
What Innovations Truly Changed the Vacuum Cooling Game?
You see a modern, stainless steel vacuum cooler operating flawlessly and it looks simple. But behind that easy operation are
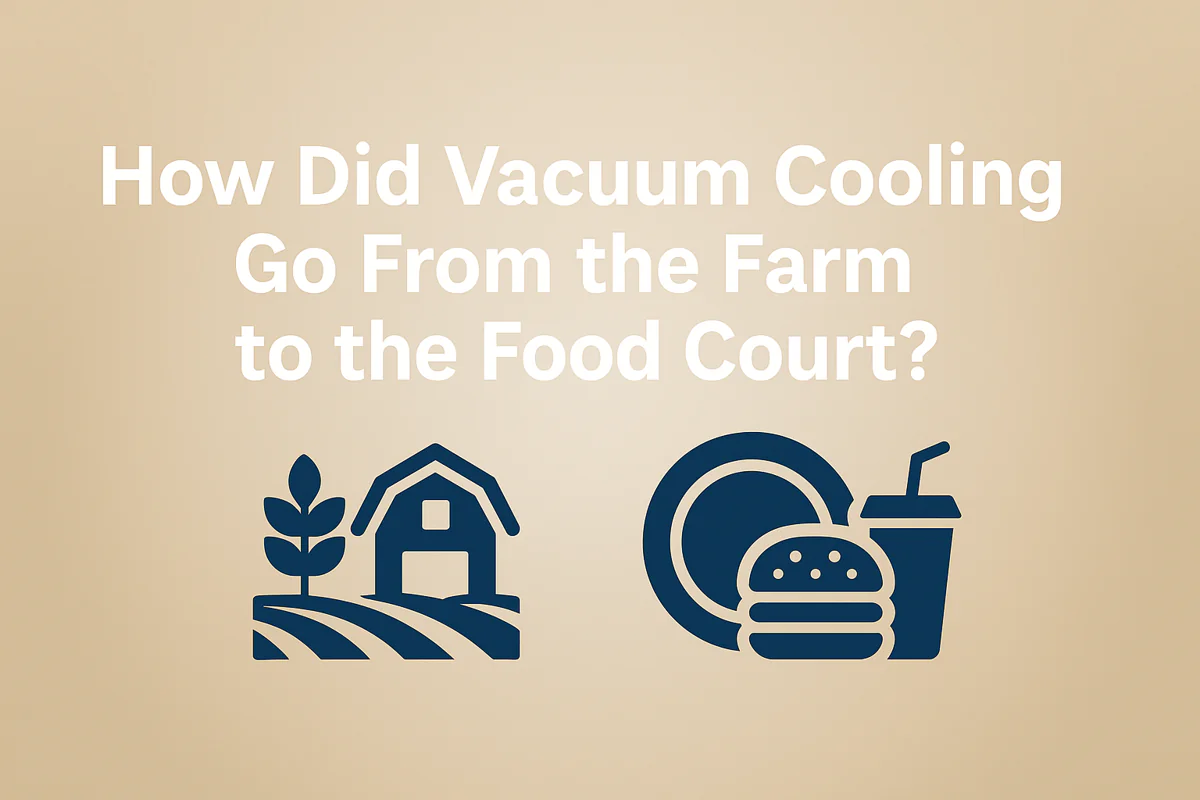
How Did Vacuum Cooling Go From the Farm to the Food Court?
You see a vacuum cooler in a modern bakery and think it’s a kitchen appliance. This powerful technology actually started
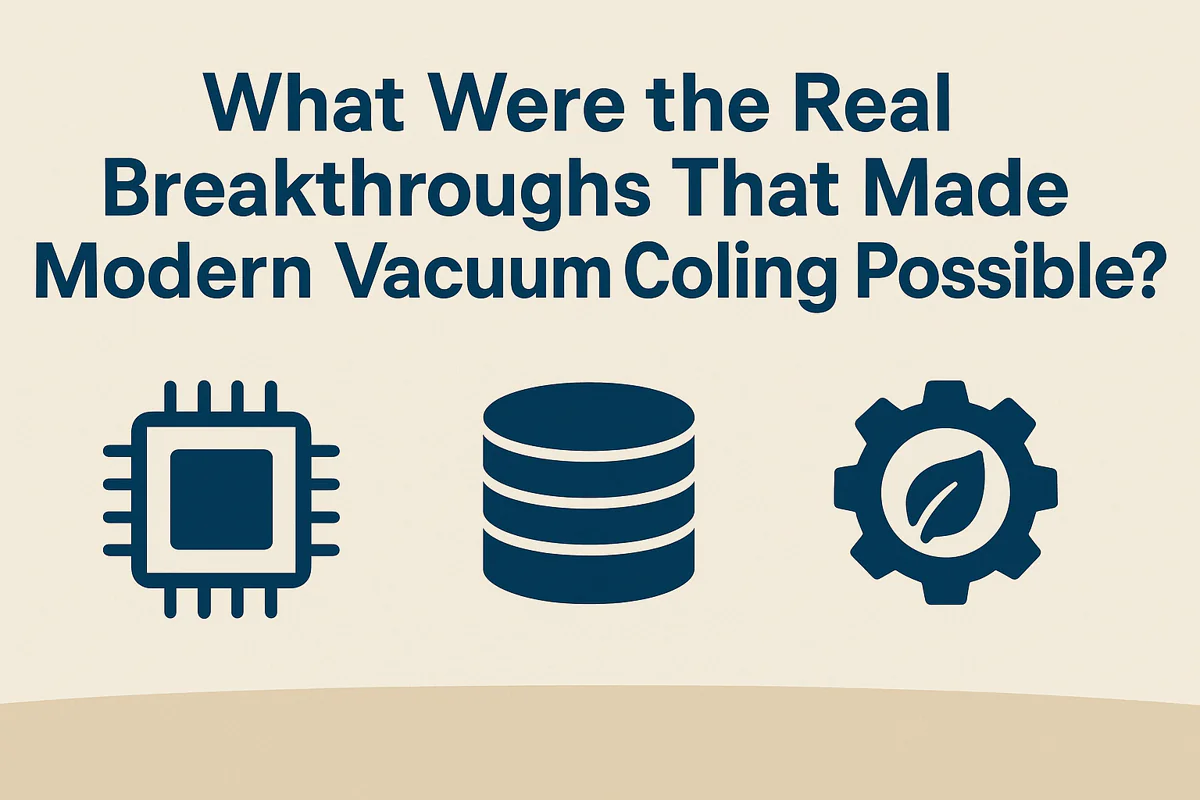
What Were the Real Breakthroughs That Made Modern Vacuum Cooling Possible?
You look at today’s advanced vacuum coolers and see a fast, reliable, and almost automatic process. It’s easy to take
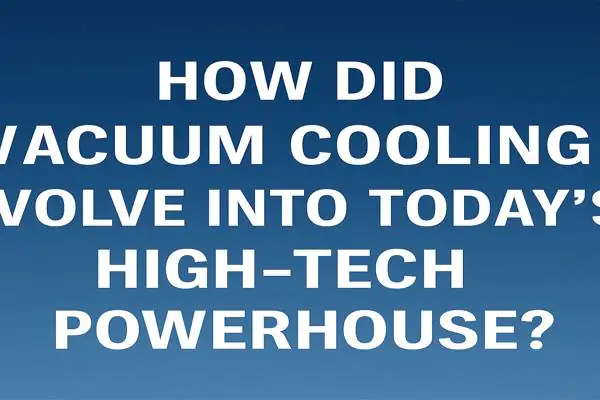
How Did Vacuum Cooling Evolve into Today's High-Tech Powerhouse?
You see a modern vacuum cooler: a sleek, stainless steel chamber with a complex control panel. You know it works
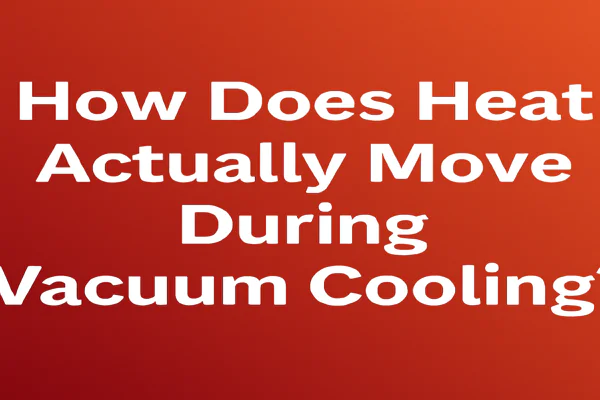
How Does Heat Actually Move During Vacuum Cooling?
You have a big challenge: a mountain of product, full of heat. You know that getting this heat out quickly
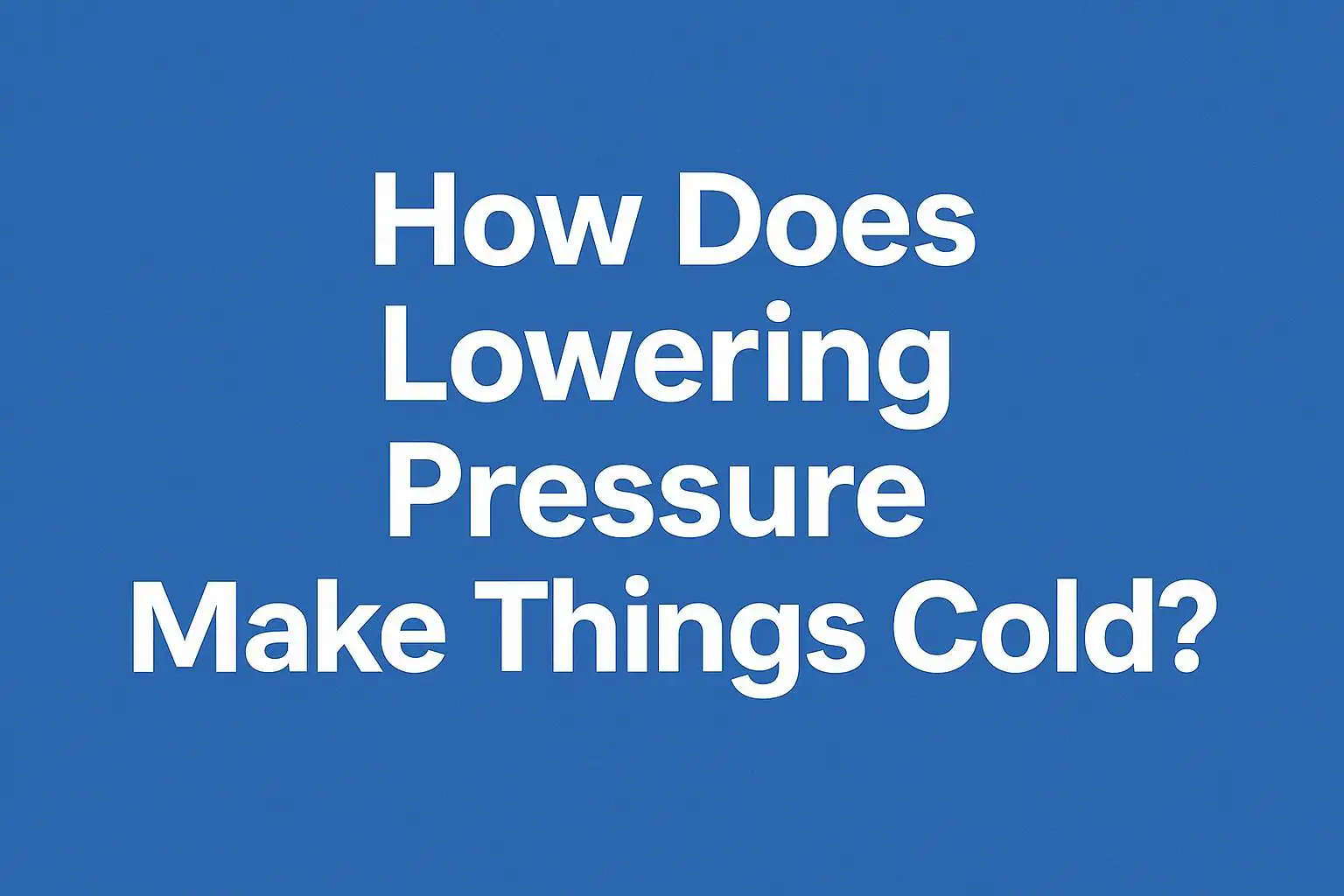
How Does Lowering Pressure Make Things Cold?
You look at the control panel of a vacuum cooler, seeing a pressure gauge dropping while a temperature gauge follows
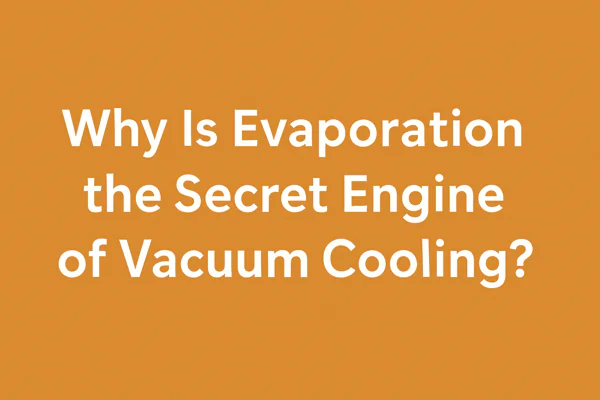
Why is Evaporation the Secret Engine of Vacuum Cooling?
You see a pallet of hot, freshly baked bread or warm, just-picked spinach. You know that slow cooling means lower
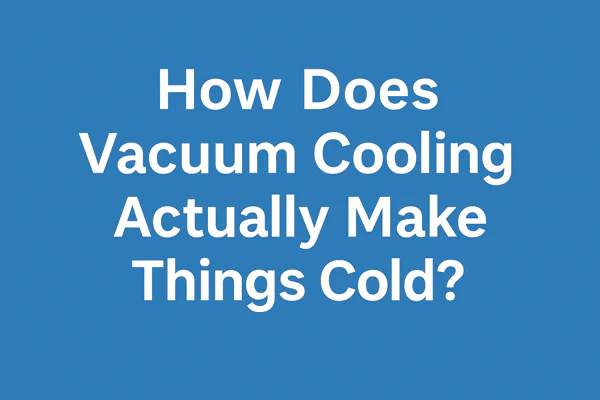
How Does Vacuum Cooling Actually Make Things Cold?
You’re looking at a pallet of freshly harvested lettuce, warm from the field. You’re told a machine can make it