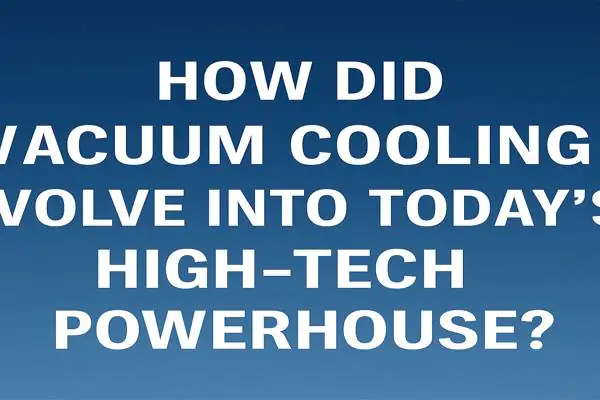
How Did Vacuum Cooling Evolve into Today's High-Tech Powerhouse?
You see a modern vacuum cooler: a sleek, stainless steel chamber with a complex control panel. You know it works wonders, but it’s easy to assume this technology appeared overnight. How did we get from a basic scientific idea to this advanced, reliable machine?
Today’s vacuum cooler is not a single invention but an evolution. It combines decades of refinement in specialized components sourced from global leaders in engineering, all integrated by a smart, user-friendly control system to meet very specific industry needs.
The core principle—that water boils at a lower temperature under reduced pressure—hasn’t changed. However, the machine built around that principle has transformed completely. It’s a story of international collaboration, precise digital control, and a relentless focus on solving real-world problems for producers like you. Let’s look at the key developments that made this possible.
How Did Machines Evolve from a Single Origin to a Global Assembly?
In the early days of any technology, machines are often built with parts from a single country or manufacturer. This limits performance to that one company’s expertise. You might get a great pump but a mediocre control system. The result? Unreliable performance.
The modern vacuum cooler broke this mold. It evolved into a "best-of-breed" system, integrating premier components from specialized manufacturers around the world to ensure every single part of the machine is world-class.
When I design a machine for a client, I’m not just building it in our factory in Dongguan, China. I am orchestrating a global symphony of engineering excellence. The goal is uncompromising quality. We build the stainless steel vacuum chamber and perform the final assembly, but the critical internal components are sourced from the companies that do one thing and do it better than anyone else. This philosophy is a major leap from early single-source machines. By combining the best parts, we create a machine that is more powerful, efficient, and reliable than the sum of its parts. For a quality-sensitive buyer, seeing this list of brands provides immense confidence in the machine’s longevity and performance.
A Global Team of Components
Component | Brand(s) | Country of Origin | Role in the Machine |
---|---|---|---|
Compressor1 | Bitzer | Germany | The heart of the refrigeration system that cools the ice-catcher. |
Vacuum Pump | Leybold / Nash | Germany / USA | The engine that removes air to create the vacuum. |
Valves & Controls | Danfoss | Denmark | Precisely controls the flow of refrigerant for maximum efficiency. |
Electrical Systems | Schneider | Germany / France | Ensures reliable and safe distribution of electrical power. |
PLC & Touch Screen2 | Siemens | Germany | The "brain" that automates the entire cooling cycle. |
Safety Components | Carlo Gavazzi | Switzerland | Provides critical protection for the electrical systems. |
How Did the Technology Adapt for Different Industries?
Early industrial equipment was often blunt and generic. A machine did one thing, and you had to adapt your product to fit the machine. Today, that is completely reversed. The market demanded that the technology adapt to serve diverse and highly specific needs.
Vacuum cooling evolved from a general concept into a wide range of specialized machines designed for specific products, from delicate produce and mushrooms to high-temperature baked goods.
This evolution was driven by my clients’ needs. A mushroom farmer has a different challenge than a commercial baker. The technology had to become flexible. For example, one of our machines is designed to take a 300 kg pallet of mushrooms and cool it in about 20 minutes. Another is built specifically for a Hungarian bakery, designed to cool 200 kg of freshly baked bread from a blistering 92°C down to 30°C in less than 5 minutes. These are vastly different tasks requiring different cycle parameters, chamber dimensions, and even system features. We now design machines based on trolley or pallet dimensions, total weight per cycle, and the product’s unique characteristics. This has led to the development of specialized features like the "vacuum delay facility3," which can be used for products that have a higher resistance to giving up their water, ensuring uniform cooling throughout the entire load. This shift from a generic cooler to a custom-designed solution4 is a key part of the technology’s modern history.
How Did Machine Control Become So Smart?
Imagine trying to operate a powerful machine using only manual switches and analog gauges. It would be difficult, inconsistent, and prone to error. The biggest leap forward in usability and performance has been the integration of sophisticated digital controls.
The evolution from manual operation to automated PLC control with a touch screen interface has revolutionized vacuum cooling. It allows for simple, repeatable, and perfectly precise operation, taking the guesswork out of the process.
The "brain" of every modern Allcold machine is a Siemens PLC (Programmable Logic Controller)5. This is a rugged industrial computer that we program with the exact parameters for your product. The operator doesn’t need to be a physicist; they just use the simple touch screen control. This interface provides a real-time view of the entire cycle, displaying the vacuum level, product temperature, and elapsed time. It makes a complex process incredibly simple to manage. But the intelligence goes deeper. The PLC automates complex sequences that optimize performance and efficiency. For example, instead of drawing a massive amount of electricity by starting all the motors at once, the system uses a "start sequence / power save6" feature. It automatically staggers the motor start-up to minimize the peak load on your factory’s electrical supply. This level of intelligent control also allows for automatic cooling cycles and other advanced features that simply weren’t possible in the early days of the technology. It’s a true evolution from a brute-force mechanical process to a smart, refined system.
When Did Safety and Efficiency Become Top Priorities?
Just making something cold is not enough in the modern industrial world. A machine must also be safe for its operators, protect itself from damage, and use energy as efficiently as possible. This focus on safety and efficiency is a hallmark of modern design.
Modern vacuum coolers have evolved to include a comprehensive suite of safety and efficiency systems. These range from emergency stops and protection relays to high-efficiency components that minimize power consumption.
Building a safe machine is paramount. Our designs incorporate multiple layers of protection. We use Schneider emergency stop buttons7 and safety relays, which can instantly shut down the machine in a hazardous situation. We also integrate specialized components like phase protection from Carlo Gavazzi in Switzerland, which guards the motors against damaging electrical fluctuations. This robust safety framework is a critical evolutionary step. Alongside safety, efficiency has become a major driver of design. Energy is a significant operational cost, so we have focused on optimizing every part of the system. We use high-efficiency evaporators8 and air-cooked condensers to get the most cooling power from the least amount of electricity. We pair world-class compressors like Bitzer with perfectly matched vacuum pumps from Leybold or Nash to ensure the system runs at its peak performance without wasting power. This holistic approach—where safety and efficiency are considered just as important as cooling speed—is what defines a truly modern, evolved piece of industrial equipment.
Conclusion
The modern vacuum cooler is a story of evolution. It stands on the shoulders of global engineering giants, driven by intelligent control systems and designed for the specific, diverse needs of modern food production.
-
Understanding the function of a Compressor is crucial for optimizing refrigeration efficiency. ↩
-
Exploring PLC and Touch Screen technology can enhance your knowledge of automation in cooling systems. ↩
-
Understanding the vacuum delay facility can enhance your knowledge of specialized cooling solutions for various products. ↩
-
Exploring custom-designed solutions can reveal how tailored machinery improves efficiency and meets specific client needs. ↩
-
Explore this link to understand how Siemens PLC enhances automation, efficiency, and control in modern industrial applications. ↩
-
Learn about the start sequence / power save feature to see how it optimizes energy consumption and improves operational efficiency. ↩
-
Explore how Schneider emergency stop buttons can significantly improve safety in industrial machines, ensuring quick response in emergencies. ↩
-
Learn about high-efficiency evaporators and their role in reducing energy costs while maximizing cooling performance in industrial applications. ↩
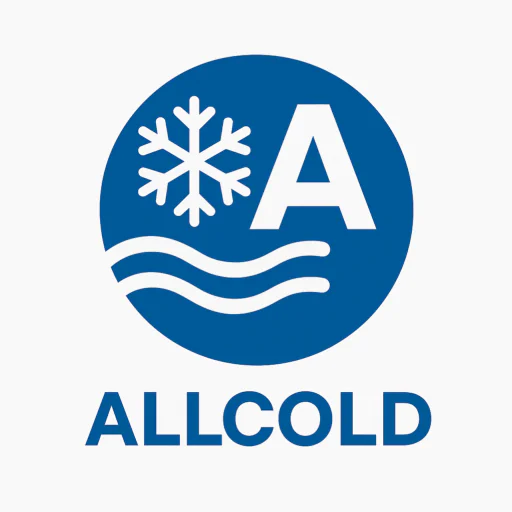
Mila
You May Also Like
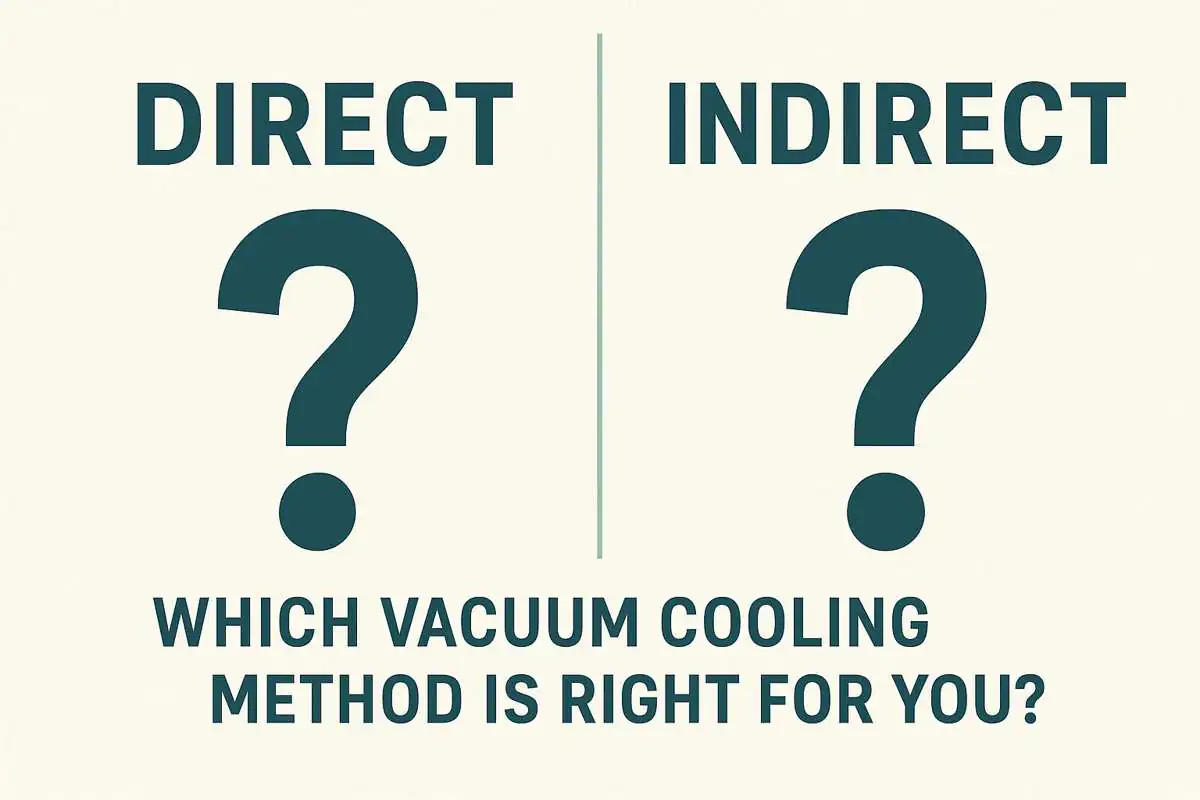
Direct vs. Indirect: Which Vacuum Cooling Method is Right for You?
You’ve decided on vacuum cooling, but a hidden technical choice emerges: direct or indirect cooling. This single design decision can
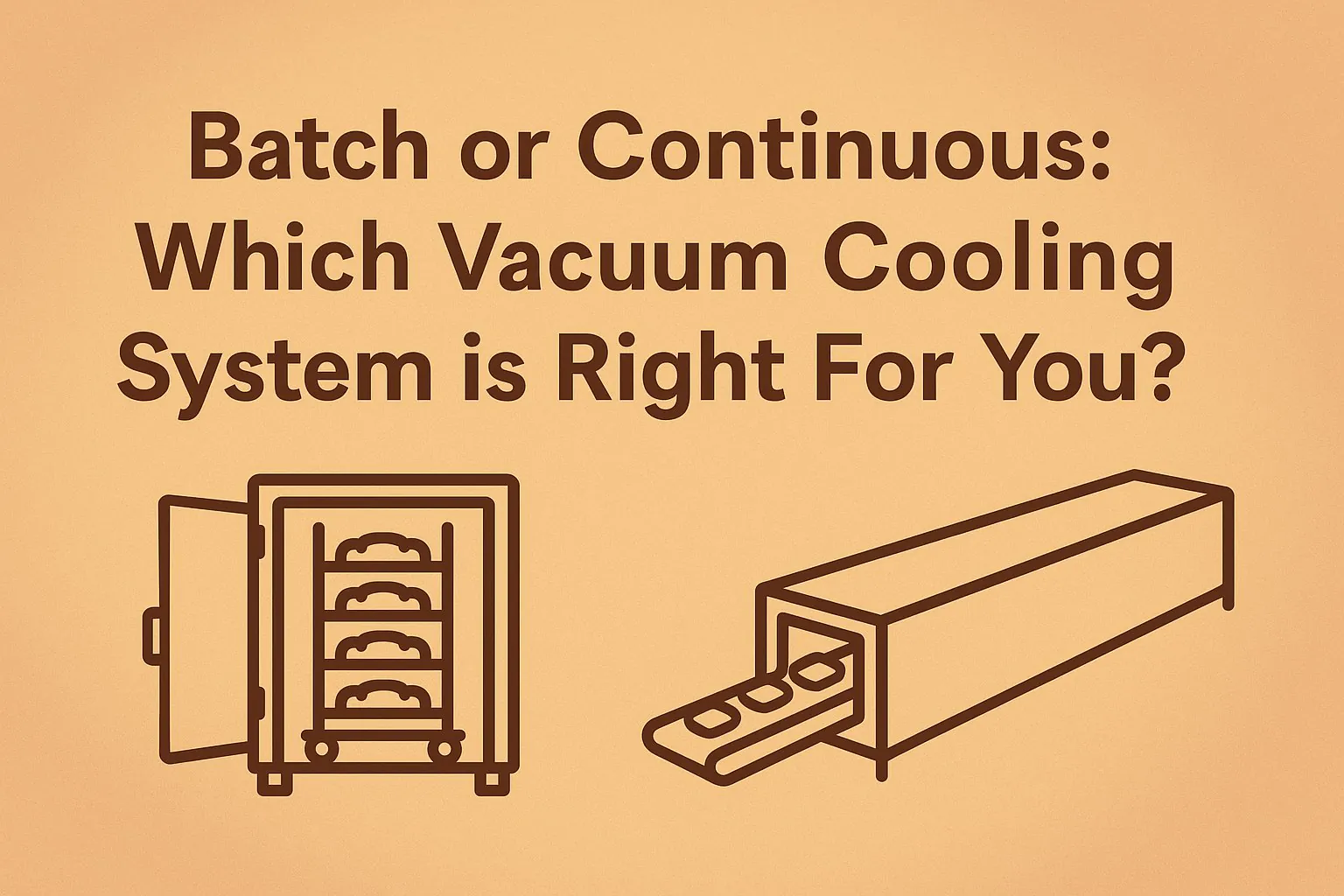
Batch or Continuous: Which Vacuum Cooling System is Right For You?
Choosing a major piece of equipment can be daunting. You know you need vacuum cooling, but then you see terms
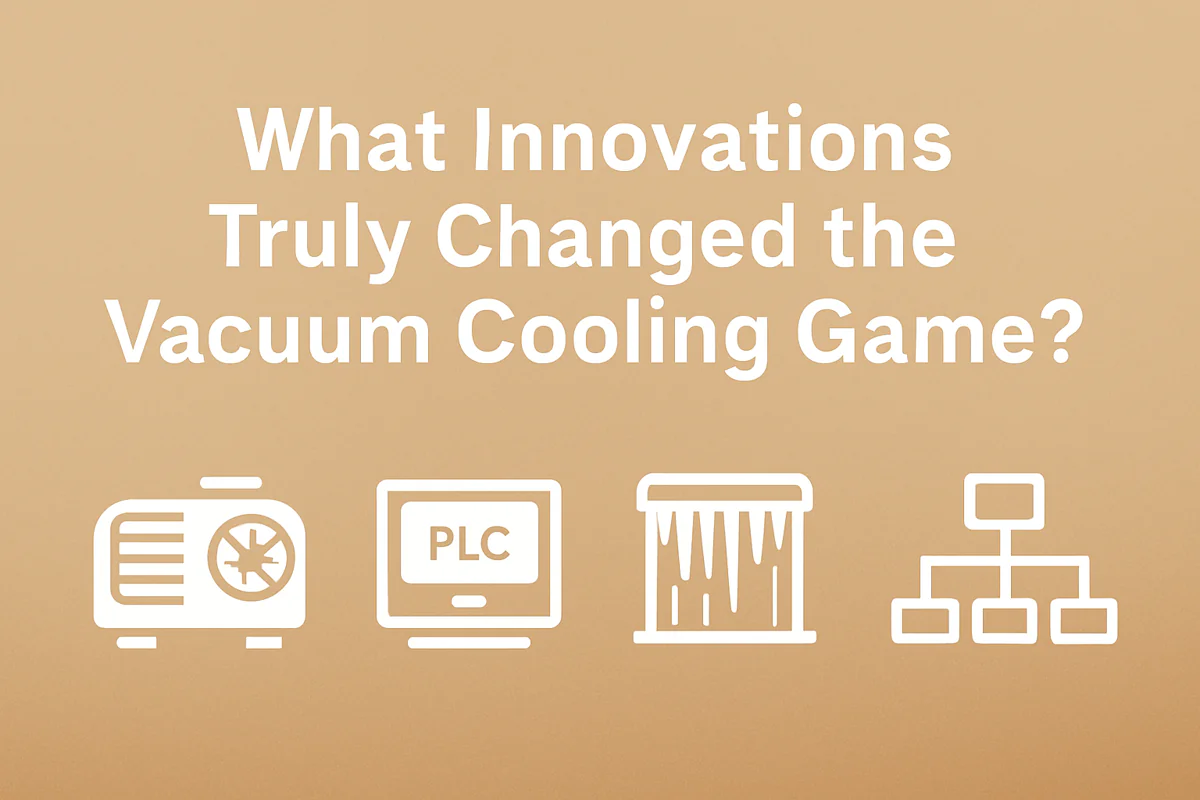
What Innovations Truly Changed the Vacuum Cooling Game?
You see a modern, stainless steel vacuum cooler operating flawlessly and it looks simple. But behind that easy operation are
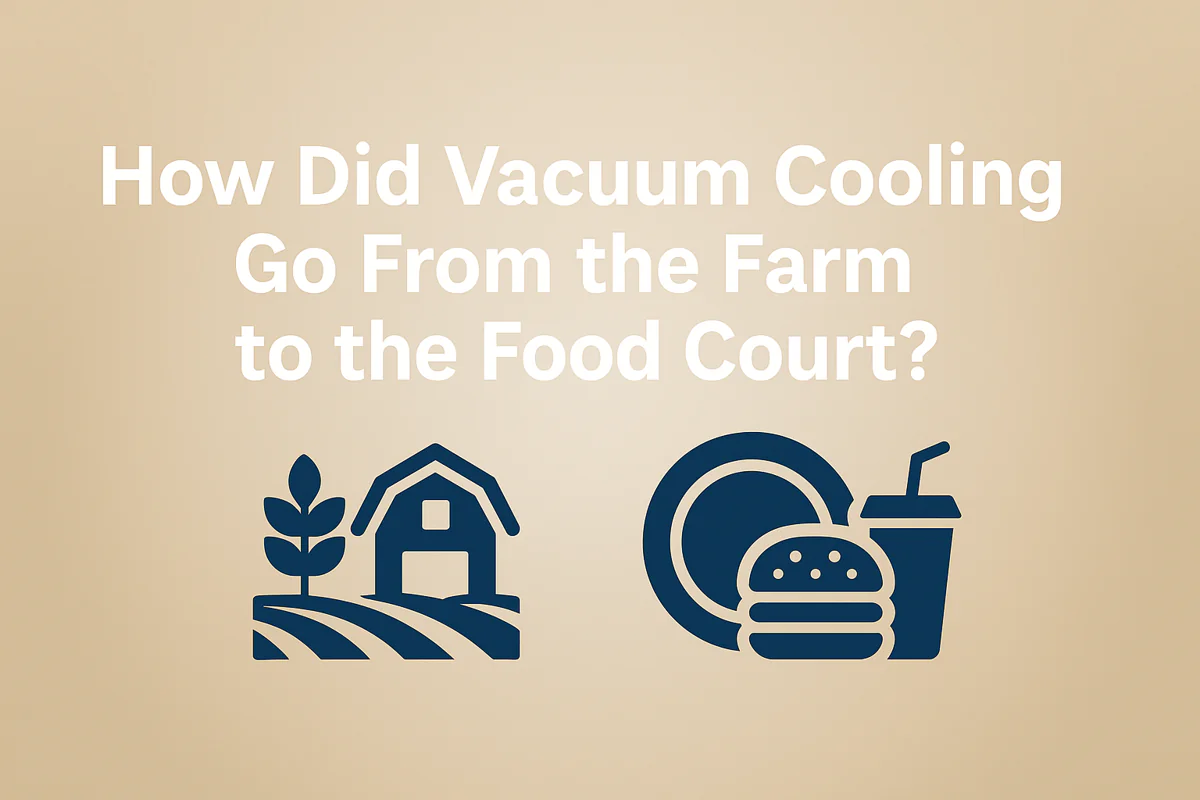
How Did Vacuum Cooling Go From the Farm to the Food Court?
You see a vacuum cooler in a modern bakery and think it’s a kitchen appliance. This powerful technology actually started
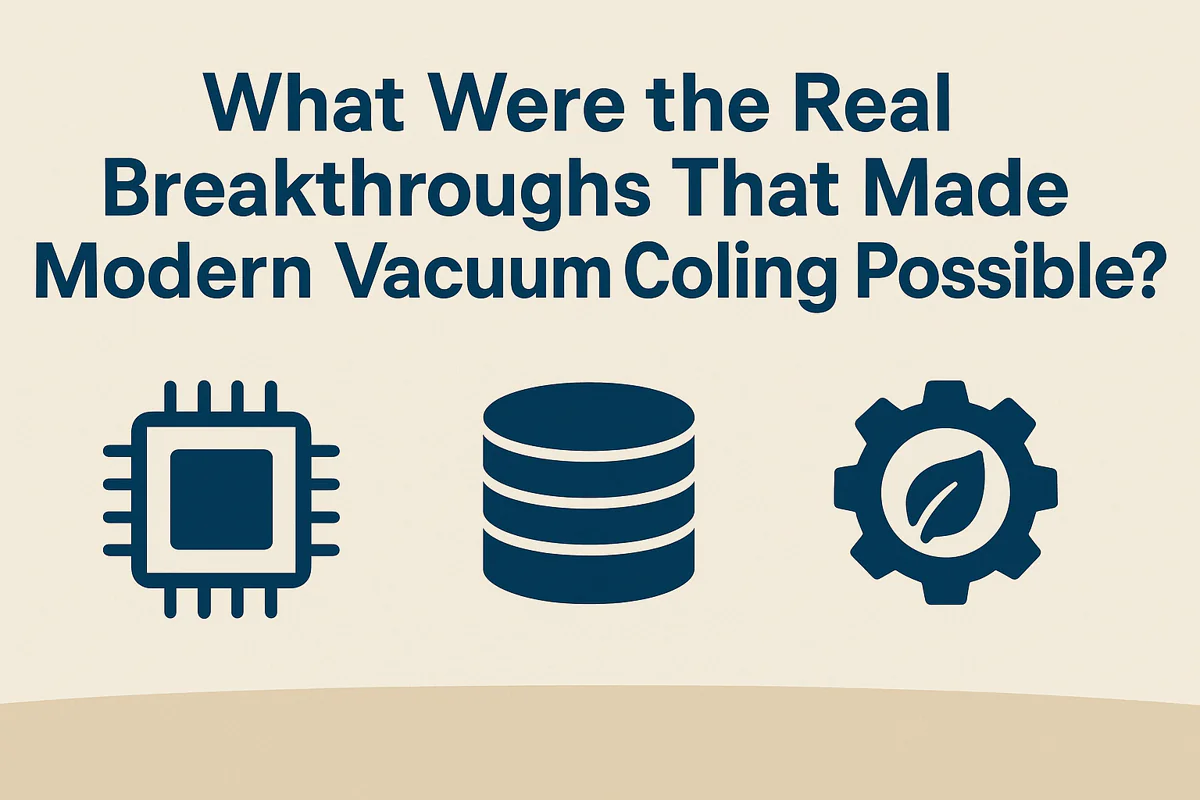
What Were the Real Breakthroughs That Made Modern Vacuum Cooling Possible?
You look at today’s advanced vacuum coolers and see a fast, reliable, and almost automatic process. It’s easy to take
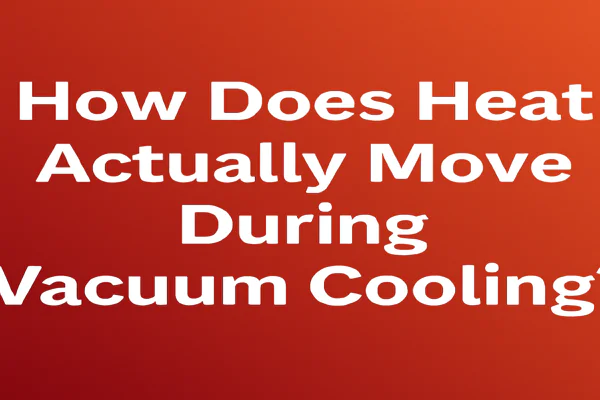
How Does Heat Actually Move During Vacuum Cooling?
You have a big challenge: a mountain of product, full of heat. You know that getting this heat out quickly
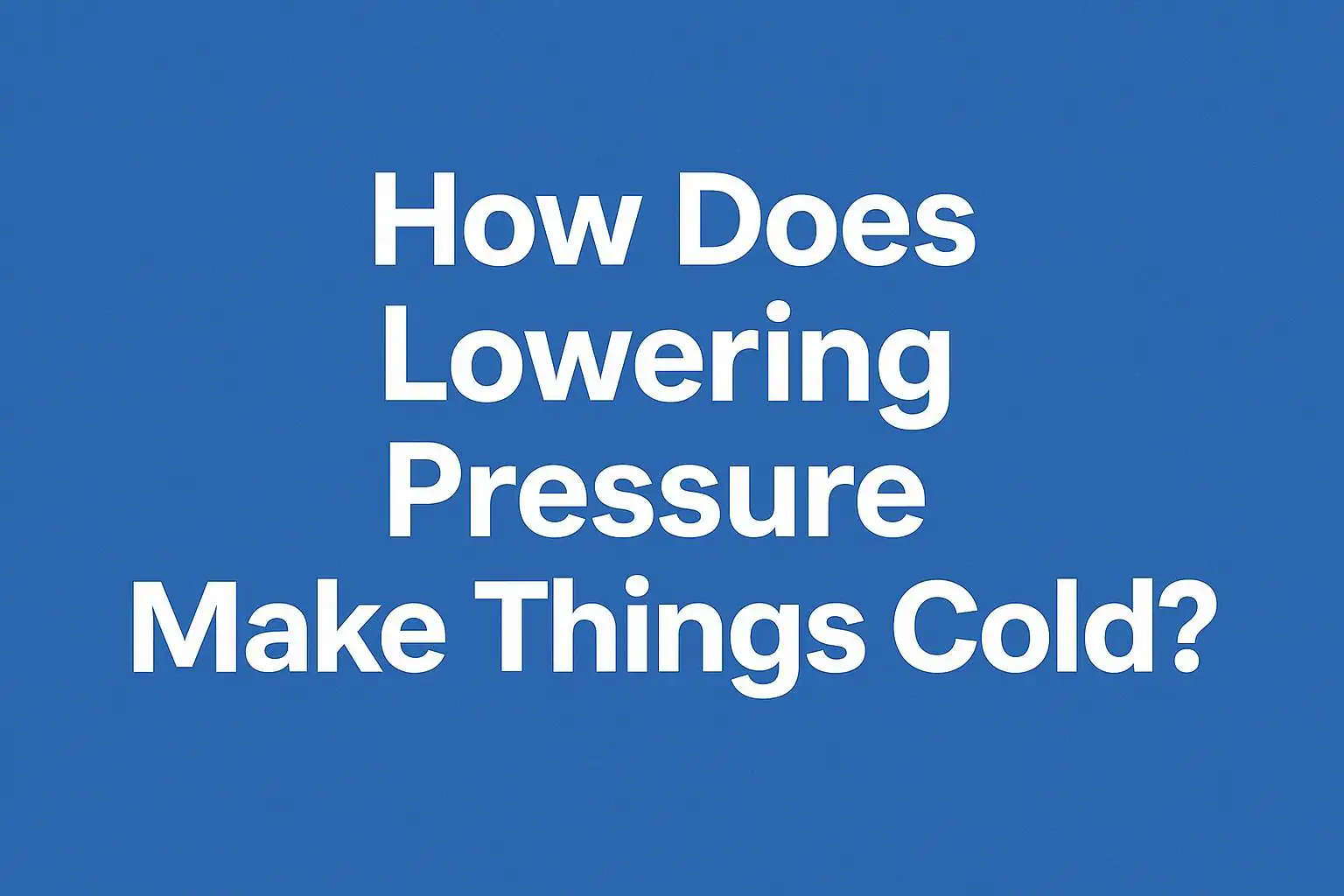
How Does Lowering Pressure Make Things Cold?
You look at the control panel of a vacuum cooler, seeing a pressure gauge dropping while a temperature gauge follows
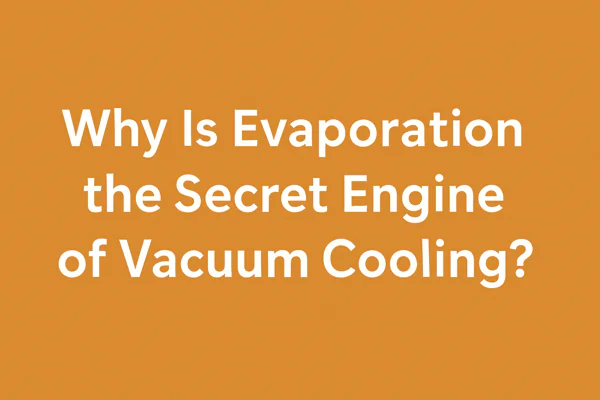
Why is Evaporation the Secret Engine of Vacuum Cooling?
You see a pallet of hot, freshly baked bread or warm, just-picked spinach. You know that slow cooling means lower
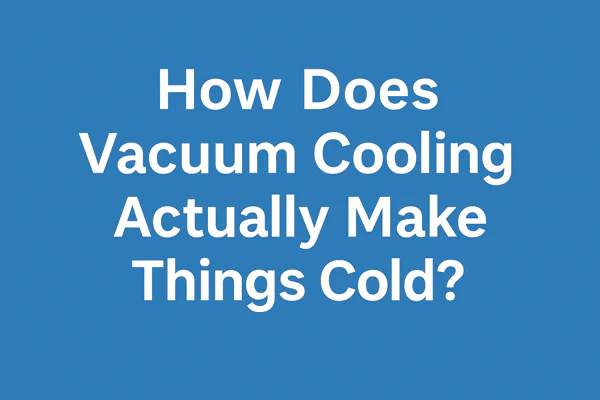
How Does Vacuum Cooling Actually Make Things Cold?
You’re looking at a pallet of freshly harvested lettuce, warm from the field. You’re told a machine can make it
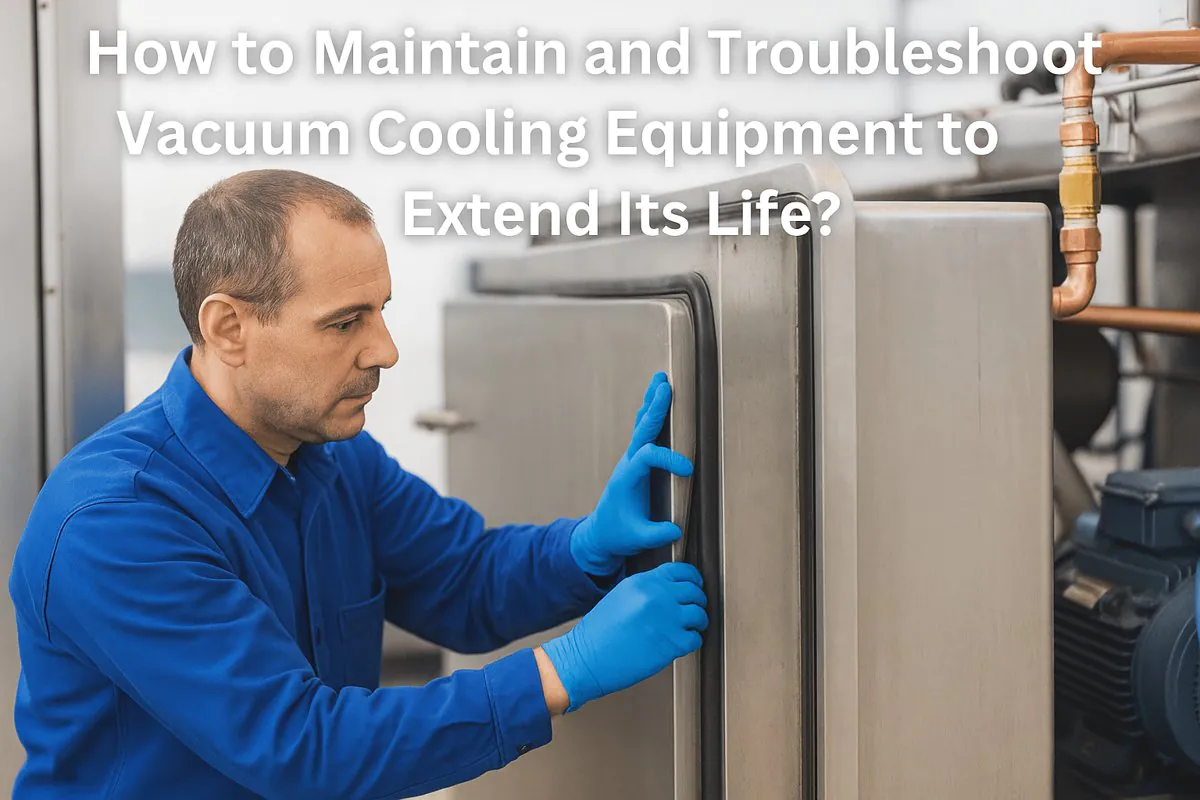
How to Maintain and Troubleshoot Vacuum Cooling Equipment to Extend Its Life?
Has equipment breakdown during peak seasons cost you dearly? Neglecting regular maintenance often leads to unexpected and costly downtime. Effective